Screen Printing Simulated Process on a Manual Press from Start to Finish
Screen Printing Courses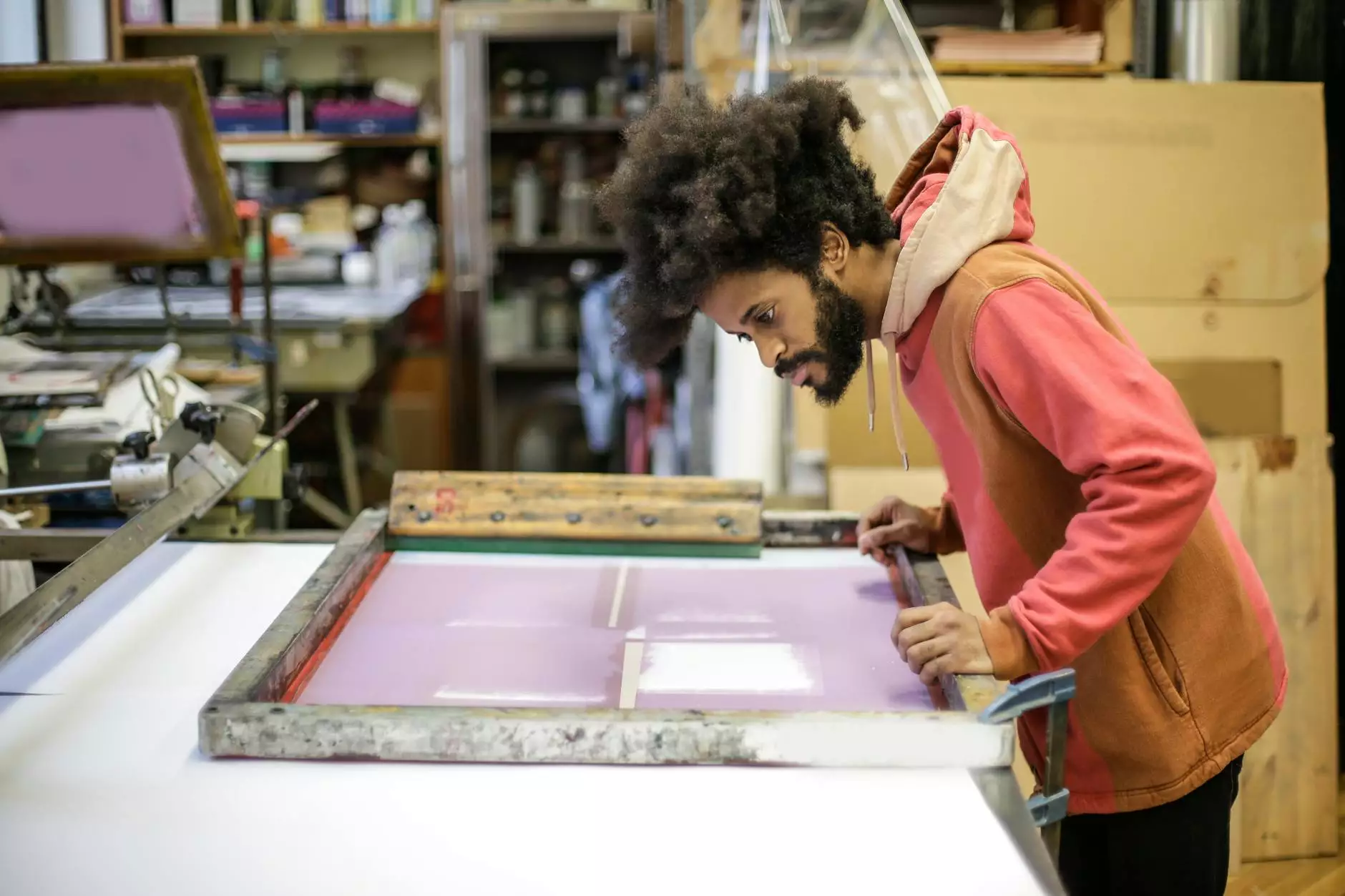
Introduction
Welcome to KTX Marketing, your go-to destination for top-notch digital marketing services in the Business and Consumer Services industry. In this detailed guide, we will walk you through the intricacies of screen printing simulated process on a manual press, providing you with valuable insights and step-by-step instructions.
What is Screen Printing Simulated Process?
Screen printing simulated process involves using a manual press to create vibrant and detailed designs on garments. This technique allows for the reproduction of complex, photorealistic designs by utilizing a limited number of spot colors. It is a popular choice for businesses looking to create visually striking and high-quality prints.
The Process
Step 1: Design Preparation
Before diving into the screen printing process, it is essential to prepare the design. Start by selecting the artwork and ensuring that it is suitable for simulated process printing. This involves evaluating the color separations and determining the spot colors required to achieve the desired effect.
Step 2: Choosing the Right Garments
When working with simulated process printing, it is crucial to select garments that can showcase the intricacies of the design. Consider factors such as fabric color and composition to ensure optimal results. High-quality garments provide a solid foundation for the entire printing process.
Step 3: Screen Preparation
Next, it's time to prepare the screens. Coat the screens with a light-sensitive emulsion, then expose them to UV light with the designs placed on top. This process creates the stencil necessary for printing. Rinse the screens carefully to wash away any excess emulsion and wait for them to dry before moving on to the next step.
Step 4: Press Setup
Now it's time to set up the manual press. Adjust the platen height and tension, ensuring that the screens align perfectly with the printing surface. Use registration marks to facilitate accurate placement of the design on the garments. Take the time to make any necessary adjustments before proceeding.
Step 5: Ink Mixing
Ink mixing is a crucial step in achieving the desired color accuracy and vibrancy. Use the spot colors determined during the design preparation stage and mix them according to the specified ratios. It's important to achieve consistency in color across multiple prints.
Step 6: Printing Process
Now comes the exciting part - the actual printing process. Load the screen with the mixed ink and position it correctly over the garment. Apply the ink with a firm, even pressure using a squeegee, ensuring complete coverage. Repeat this step for each color, taking care not to smudge or distort the design.
Step 7: Curing
To ensure the longevity of the print, it's crucial to cure the ink properly. Place the printed garments through a conveyor dryer or heat press, following the manufacturer's instructions. This step ensures that the ink bonds securely with the fabric, resulting in a durable and vibrant print.
Step 8: Quality Control
Once the printing and curing processes are complete, it's time for quality control. Inspect the finished prints for any imperfections, such as smudges or color inconsistencies. Make necessary adjustments and reprints if required to uphold the highest standards.
Conclusion
Screen printing simulated process on a manual press is a meticulous and rewarding process that allows for the creation of stunning, photorealistic designs. At KTX Marketing, our team of experts is well-versed in this technique and equipped to deliver exceptional results for your business. Contact us today to learn more about our digital marketing services and how we can elevate your brand through quality screen printing.